Additive Manufacturing
Complex Structures with Additive Methods
Unlike casting or most ablative processes, additive methods allow the same machine to produce a wide variety of products without having to replace a single tool. The template that was transferred as a CAD file is all that matters. Complex geometric shapes can also be implemented in a short time.
Different Methods
of Additive Manufacturing
The suitability of different methods of additive manufacturing depends on the material and objective. Now that “3D printing” has been historically established for a long time in the processing of plastics, it is now increasingly gaining ground in the production of metal parts.
Companies in Germany rely especially on the laser beam melting process. Metal powder is typically applied to a working surface in thin layers of 20-60 µm. A laser beam melts the material specifically at the points where a solid structure is to be created.
Lasered on Top of Each Other Layer by Layer. The base plate is then lowered accordingly so that a new layer of powder can be applied. This creates the desired structure layer by layer. After processing, the excess unprocessed powder is removed. In contrast to conventional manufacturing processes, casting molds and tools are not required in additive manufacturing. This accelerates production and enables an almost infinite variety of shapes.
Laser Beam Melting
For an almost infinite variety of shapes
In laser beam melting, the metal powder is almost completely melted, resulting in a body with a specific density of >>99%. This means that many of the mechanical properties correspond to those of conventionally processed metal. However, this procedure is not yet suitable for all conventional materials because some metals change their physical properties during processing. Changes in the surface tension or viscosity of the material can lead, among other things, to the parts not meeting the quality specifications.
Laser Power Makes the Difference. Laser power is one of the deciding factors in making these technologies suitable for mass production. Among other things, stronger lasers lead to potentially higher build-up speeds (cm³/h) in the laser beam melting process. As a rule, solid-state lasers, diode lasers, and medium-strength single-mode fiber lasers with outputs of several hundred watts are used in additive manufacturing. By using several lasers at the same time, the efficiency can be additionally increased.
A slightly widened beam profile is common and results in fewer splashes and metal powder that evaporates less. It is also important that the beam not increase further due to the laser-induced focus shift (heating of the optical elements) to prevent the layers from not being completely melted.
Let us select the Ideal Laser Optics for your Application.


Single Pieces or Small Series
Uniqueness
At present, additive manufacturing processes are still frequently used for single pieces or small series. This is where the advantages of this technology make it unique. In medical technology, for example, titanium implants can be manufactured individually based on the physiological makeup of the patient. However, for economic reasons, most companies continue to use conventional production routes for the mass production of standard parts.
“If you try to reproduce standard components by simply using a 3D printer, you will often find that it takes longer and that the result does not meet the usual quality criteria,” explains Prof. Dr.-Ing. Jan T. Sehrt from the newly established chair for hybrid additive manufacturing at the Ruhr University of Bochum. “However, this is often not due to the technology but to the upstream work on the computer. Whoever wants to use additive manufacturing economically must also adapt the product design to this technology. It is best if the designer has knowledge of the entire process chain, including the use of components.”
In order to achieve an optimal result, many factors must be considered. The thicker the metal layers, the faster the product is ready. However, the “step effect” on curves, freeform surfaces, and blunt angles also increases while the surface quality decreases. It is therefore necessary to find a compromise that guarantees a high surface quality with reasonable production times.
The physical properties of the material also play a role. Anisotropic effects can occur in the component due to the layered application. Such effects can be avoided if the position of the product on the work surface is changed, for example by producing it with an incline of a few degrees. To ensure that the part is still firmly connected to the construction platform during the entire process, support structures must be included in the planning phase and then removed again after production. These struts also reduce the distortion that can occur when the material cools which affects the overall structure. They also dissipate the thermal energy generated when the powder melts.
»Whoever wants to use additive manufacturing economically must also adapt the product design to this technology.«
Prof. Dr.-Ing. Jan T. Sehrt
Chair for Hybrid Additive Manufacturing, Ruhr University of Bochum
April 2019
The Right Exposure Strategy
has a siginificant influence on product quality

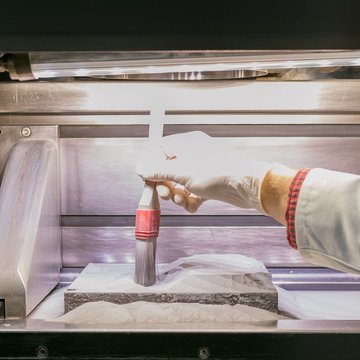
In addition to the model, the right exposure strategy also has a significant influence on product quality. Each area of a component has different requirements. Also, it is possible to set the component properties specifically via the exposure parameters with the laser. For example, a component could be built up more densely in the outer area than in the inner area.
Overhanging areas of the component play a special role because of their support structures; in certain areas a particularly high surface quality is required. These factors can be influenced by various exposure parameters – for example, the exposure time or the distance between the trails of melting. Here, too, computer programs help to determine the correct exposure strategy and thus achieve optimal product quality.
How all these measures affect the production process and product quality can be tested by the designer in a simulation on the computer before actual production begins. “As in many areas of Industry 4.0, the amount of work involved shifts from the manufacturing process to planning and control,” explains Prof. Sehrt.
Downloads
Beyond Borders
Product Selection
Beyond Borders
LASER COMPONENTS USA - Your competent partner for optical and optoelectronic components in the United States.
Welcome to LASER COMPONENTS USA, Inc., your expert for photonics components. Each product in our wide range of detectors, laser diodes, laser modules, optics, and more is worth every Dollar ($/USD). Our customized solutions cover all conceivable areas of application: from sensor technology to medical technology. You can reach us here:
116 South River Road
Building C
Bedford, NH 03110
USA
Phone: +1 603 821 7040
Email: info(at)