In State-of-the-Art, High-Tech Packaging Food Stays Fresh Longer
Fruits and vegetables are the alpha and omega of the health-conscious person of today. However, vegetables from the farmers’ market are present in fewer and fewer kitchens. Cooking and “gardening” are more like hobbies in our hectic times than daily tasks required for subsistence. Shopping should also be quick and easy. The supermarket has long since replaced the corner store because it is much more convenient to buy everything you need in one spot. It is still required that goods and produce be fresh and crisp.
Air Is a Thing of the Past
Beyond Borders
Meats, fish, fruits, vegetables, milk products, and bread – really fresh food only stays fresh a few days maximum. After that, they begin to spoil, mercilessly. How do supermarkets manage to keep the shelves stocked every day with fresh goods that look so inviting and seem to call out to us “Buy me!”?
The secret is in the packaging.
In so-called modified atmosphere packaging (MAP), the packaging is filled with a gas or gas mixture instead of air. Most commonly, nitrogen and carbon dioxide are used. Oxygen is undesired in these cases because it is not only the main cause of the oxidation-related spoiling of food but it also promotes the growth of aerobic microorganisms.
The composition of a substitution atmosphere depends on the contents of the packaging. For example, the percentage of CO2 for beef is 20%, for fish is 80%, and for pasta products is 60%. Products packaged with MAP stay fresh significantly longer – often twice as long as when stored in fresh air. They can sit on the shelves longer and do not have to be disposed of within a few days.
Protective atmospheres are not only used in comparably small supermarket portions, controlled atmospheres are also used to prevent, for example, the early ripening of bananas upon transport from Colombia to Europe. In other foods, such as milk products, manufacturers can often completely forego the use of preservatives thanks to MAP.
Sometimes holes are desired
Beyond Borders
One special challenge is packaging for fresh fruits and vegetables. After harvest, these products are still living organisms in which biochemical processes take place: the fruits “breathe” (respiration) and “sweat” (transpiration). To ensure that they stay fresh in their packaging, a small amount of oxygen must have continuous access and the CO2 produced during respiration must be able to escape.
This can be achieved via laser perforation. Microholes are burned into the packaging in a targeted manner that suits the respiratory activity of the product and regulates the oxygen content accordingly. Depending on the food and material, these holes can range in diameter between 50 µm and 300 µm.
Lasers ensure that at these small sizes a uniform perforation results that meets all of the requirements of the packaging industry.
Pulsed CO2 Lasers for Microholes
Beyond Borders
To ensure that the beam penetrates all of the layers of the packaging, CO2 lasers with high pulse intensities are most commonly used. To achieve an even distribution of the holes at exactly defined intervals, diffractive optical elements (DOEs) are used. A 15 x 15 multispot element can produce 225 partial beams from one laser beam; these partial beams burn 225 holes into a film with one shot. The size of and distance between the holes can also be changed with the help of an additional optic.
… and how do I access my food?
To maintain the protective atmosphere in the packaging, everything must be right. The majority of packaging films are so-called multilayer structures and, therefore, consist of several stacked layers.
Each material has its own function: PET, for example, is responsible for stiffness and aroma conservation; flexible but tear-resistant PE serves as a sealing medium; PP is impermeable to water vapor; and aluminum protects light-sensitive food.
Robust packaging is one thing, but the consumer does, after all, want to be able to open the package easily and without a big fight. Lasers help here, too; however, they are not used as light swords but as tools in the manufacturing of packaging.
Manufacturing Tear Strips with Lasers
Beyond Borders
The trick to so-called tear strips is to weaken the mechanical layers of the composite plastics in a targeted manner while maintaining other functions such as aroma conservation and light protection. This is possible via laser scribing.
Because the components of the composite material have different optical properties, individual layers can be processed with the laser while other layers remain intact. Computer-controlled scribing systems are most commonly used to achieve the complex designs in the material. Industrial image processing systems make correct positioning on the packaging possible. With a corresponding software program, the beam can then be controlled as necessary for each individual package.
Integrated Pressure Cooker
Beyond Borders
Laser perforation keeps food not only fresh but also makes it possible to quickly and easily prepare ready-to-eat meals. Vegetables, meat, and fish are placed together with the packaging into the microwave and cooked. The package remains closed the entire time and not even water must be added. Similar to a pressure cooker, the container builds up pressure to quickly and gently cook the contents. The trick is a valve that is integrated into the protective foil and that opens if a certain amount of inner pressure builds up to allow the steam to escape.
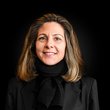
Click here
In Excellent Shape with Diffractive Optical Elements
Beyond Borders
Diffractive optical elements (DOEs) are substrates into which microstructures are etched using a lithographic process. The diffraction effects allow laser beams to be split, bundled, or formed into almost any shape. Thus, the application possibilities of DOEs are quite versatile. Unlike classic beam-shaping processes, DOEs have the advantage that the desired structures can be provided with a single optical element and the beam energy almost completely utilized. Our partner Holo/OR manufactures DOEs for application in high-power lasers.
Further Product Information
Beyond Borders
Diffractive Optical Elements
Downloads
Beyond Borders
LASER COMPONENTS France - Your competent partner for optical and optoelectronic components in France.
Welcome to LASER COMPONENTS S.A.S., your expert for photonics components. Each product in our wide range of detectors, laser diodes, laser modules, optics, fiber optics, and more is worth every Euro (€/EUR). Our customized solutions cover all conceivable areas of application: from sensor technology to medical technology. You can reach us here:
45 Bis Route des Gardes
92190 Meudon
France
Phone: +33 (0) 139 595 225
Email: serviceclient(at)