State-of-the-Art Sensor Technology in Shipbuilding
“A cruise is fun. A cruise is beautiful.” More and more tourists are convinced of this. According to a current estimate, 27 million cruises1 will be booked worldwide in 2018, which is about one and a half times as many as ten years ago.2 It is no wonder, then, that more and more, larger and larger ships are sailing the seas. The order books at the shipyards are full. Keeping the construction time of ocean giants like the “Norwegian Bliss” (see photo) as short as possible requires not only perfect project management but also means precision work with steel structures that weigh tons.
Ship Puzzle
Beyond Borders

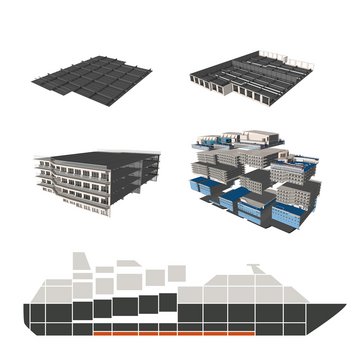
When renowned shipping companies need new cruise ships, they turn to MEYER WERFT in Papenburg. In its 223-year company history, this family-run business from Lower Saxony has repeatedly proven that pioneering spirit and belief in new technologies pay off.
When Josef L. Meyer decided in the 1870s to focus resolutely on the construction of steam-powered steel ships, many Papenburg shipping company and shipyard owners looked upon him with mild amusement. History has proven him right: In the 19th century, there were about twenty shipbuilding companies in the city, and of them only MEYER WERFT has survived to this day.
The decision to start building luxury cruise ships has also proven to be the right one. In 1984, when the company accepted the order for the ocean giant "Homeric", this outcome could not have been foreseen. The project was a risk and associated with many technical challenges. For example, a new lock had to be built specifically for the purpose of removing the ship from the dock when it was finished.
From Small to Large
Beyond Borders

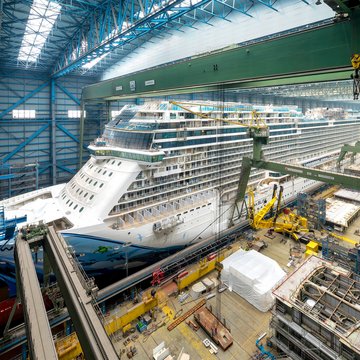
MEYER WERFT is still one of the most modern shipbuilding facilities in the world. Following the principle of modular construction, the production of luxury liners such as the “Norwegian Bliss” takes just nine months from when the keel is laid to launch. By comparison, this new ship is about four times the size of the "Homeric", which was completed in 1985 and spent a year in the building dock at the time.
In modular construction, small partial elements are prefabricated and then assembled into ever larger units: Initially, individual steel plates are painted with a sealant to protect against corrosion, cut to size with a plasma burner, and welded together to form panels. Other components that are important at a later stage for the operation of the ship are also manufactured in advance. This means that production of these individual parts can begin immediately after the order has been accepted while the building docks are still occupied by other ships.
The heart of steel construction is the automated panel line. There, the cut steel plates with profiles, beams, and side walls are processed into so-called sections. The thermal insulation, as well as the cable wiring and piping packages, in which up to 250 km of electricity and water pipes will run later, are also laid now. The production facility works, so to speak, in a figurative headstand. The steel plates, to which all other elements are attached, serve as cabin ceilings in the completed ship, the cable ducts and pipes are used to supply the cabin above. Every four hours a finished section leaves the production hall.
A Precision Job for Strong Men
– FROM SECTION TO BLOCK

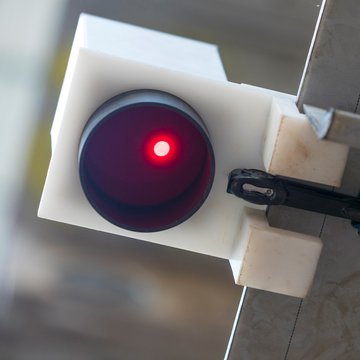
This time remains for shipyard workers to assemble the finished sections into the next larger units. About eight to ten of them form a block that extends across the entire width of the ship. The blocks are up to 37 meters long and up to six decks high. In order to form a perfect unit, the individual sections must be positioned exactly. This is done manually. Since a crane is too inaccurate due to the inertia in the crosshead and rope, the shipyard workers use hydraulic traction and compression presses to fit the parts, which weigh around 160 tons, with millimeter precision.
Achieving this precision is one of the greatest challenges. Mechanical plummets were used for a long time; however, they were very susceptible to wind. They were constantly “off center” and also had to be read visually. In order to align the sections precisely, their position had to be measured in a separate work step by measuring teams using tachymeters. Then it was readjusted and measured again until the component had arrived at the right spot. “This laborious process consumed a lot of resources,” says Ralph Zimmermann, Head of Surveying at MEYER WERFT. “That’s why we’ve been looking for a state-of-the-art method for a long time. Shipbuilders should control their work as self-sufficiently as possible. At the same time, the technology had to withstand the everyday working conditions in a shipyard.”
Positioning Lasers in Action
Beyond Borders

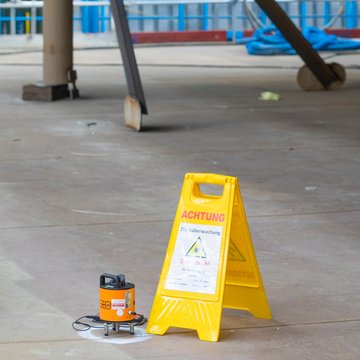
Prefabricated "off-the-shelf" solutions did not meet these requirements. After extensive tests, an optoelectronic alignment system has been in use since the autumn of 2017, which the shipyard has developed together with LASER COMPONENTS and the Neubrandenburg University of Applied Sciences. In laser-assisted alignment, four lasers each are placed on the front and rear of the hall floor and anchored with integrated bolts. These self-levelling lasers automatically level out unevenness so that the laser beam is always perpendicular. A detector is attached to the section ceiling above each laser, which evaluates the position of the beam similar to the crosshairs of a rifle scope. The data is then transmitted by radio to a display so that the shipbuilders are always informed about the exact position. When all eight beams hit their target exactly in the center, the section is in the right place and assembly can begin. In this way, the blocks are not only completed more accurately but also faster. Ralph Zimmermann is enthusiastic about the alignment system: “The positive effects on our production processes can already be clearly seen. I can no longer imagine the daily work performed at MEYER WERFT without this system.” Accordingly, the next step is already being planned. Then it is a matter of positioning the entire blocks. Up to now, costly, sensitive tachymeters have been used to assemble around 70 of these “puzzle pieces,” which weigh up to 800 tons, into a ship. Here, too, lasers could soon point the way.

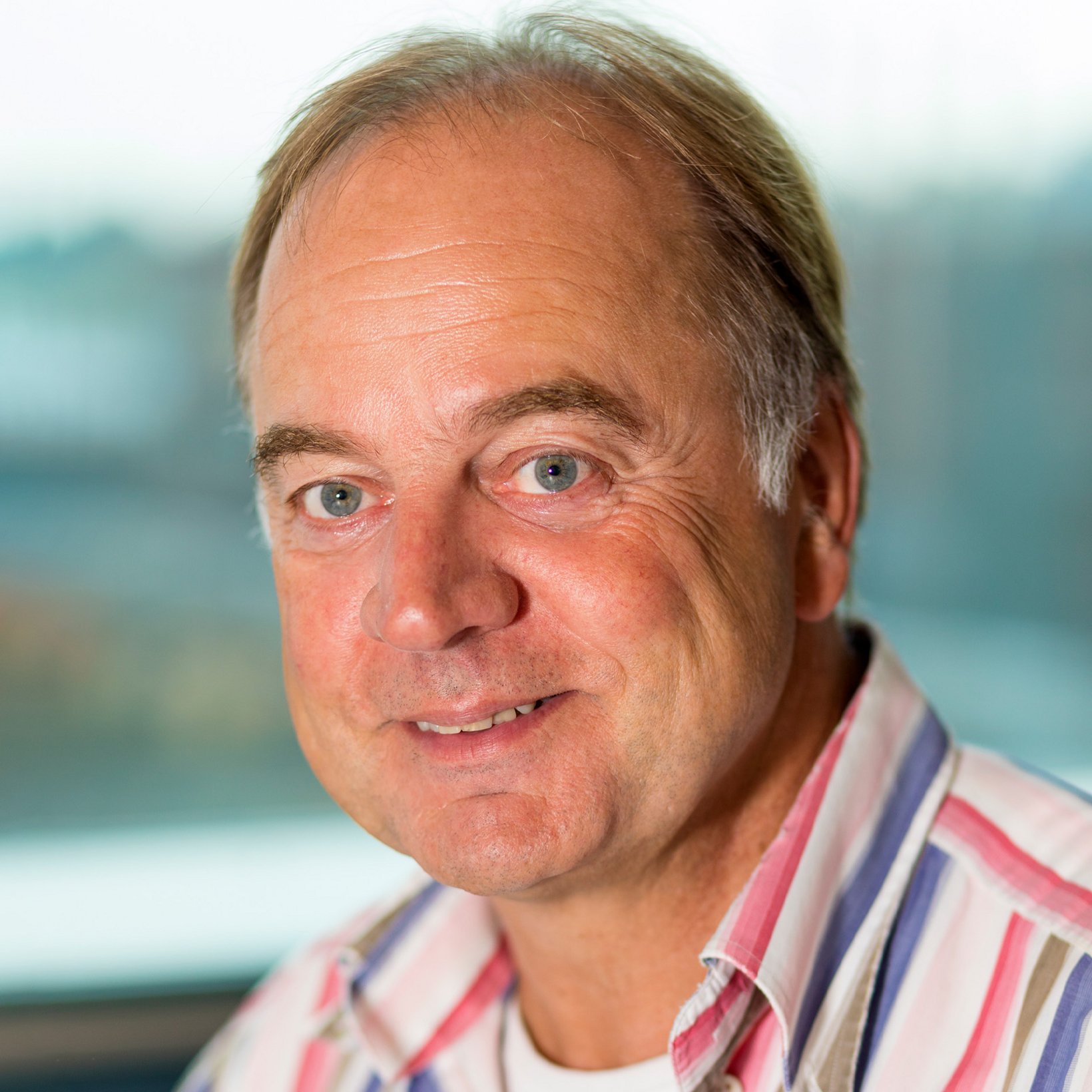
“Producing a modular cruise ship for 4,000 passengers means assembling many individual pieces with millimeter precision. Traditional methods are complex, cost time, and require a lot of personnel. With state-of-the-art laser technology, we can work much more precisely and efficiently nowadays.”
Ralph Zimmermann,
Head of Surveying at MEYER WERFT in Papenburg
1 http://www.cliadeutschland.de/pdf/2017/35-15.12.2017_CLIA-Outlook-of-the-Industry_Praesentation.pdf
2 https://de.statista.com/statistik/daten/studie/168360/umfrage/passagiere-auf-kreuzfahrten-weltweit/
Success in the Application
Beyond Borders
Norwegian Bliss
The Norwegian Bliss undocked on February 19, 2018. Transfer to the North Sea began on March 13, 2018. At only 0.2 knots, the 333.4-meter-long and 41.4-meter-wide ship was discharged from the MEYER WERFT shipyard and steered backwards towards the sea on the Ems River for better maneuverability. In June, the “Breakway Plus” class ship will set sail from Seattle for a seven-day cruise to Alaska. From November they will be found in the eastern Caribbean.
This ship is one of the most state-of-the-art cruise ships. 27 dining options, a theater with over 800 seats, the longest (electric) go-cart track at sea, a 180-degree panorama observation lounge, multi-story water slides – one of which goes beyond the railing – and many more attractions promise guests an unforgettable journey. More than 1,700 crew members ensure the well-being of the approximately 4,000 passengers.
Such Theatrics!
Did you know that MEYER WERFT is the largest German theater builder? Today, every modern cruise ship has at least one large theater hall with up to 1,000 seats, a fly tower for changing sets, and a retractable orchestra pit. This is why MEYER WERFT has built more theaters than any other company in Germany.
Precise Adjustment across Long Distances
Beyond Borders
With the STRAIGHTliner FAR laser alignment system, components can be positioned across distances of up to 200 m with millimeter precision. This is important not only in shipbuilding but also in the alignment of machines, rails, cranes and elevators.
The system features a long-range laser module that can be focused to a point that has a diameter of less than 15 mm at a distance of 200 m. The equipment also includes the wireless connection of an extra-large detector to a PC and intuitive Windows software with graphical user guidance.