Lasers Easily Make Tough Measurements in Automobile and Aircraft Manufacturing
As creative innovators in the automobile and transport industries continue to drive for new solutions to old manufacturing problems, dot, line and patterned laser modules continue to move technology into the future. Where rotational wobble threatens with wear, tear and lowered performance efficiency, the exactness of the dot or line laser can quickly ensure optimal alignment in the manufacturing process. Where gaps and seams threaten mechanical integrity, the line laser can raise the flag before the problem leaves the factory. In an era where superior engineering is signified by alluring body design, the ideal 3D form analysis can be generated by the right diffractive optical element and laser module.
Dot Lasers for Alignment Tasks
Beyond Borders

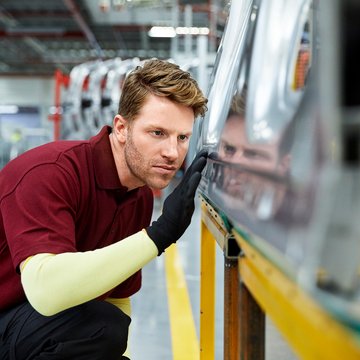
How many different ways can a part on an automobile or aircraft wobble, vibrate, deflect, compress, disconnect and so on? Mechanical tools necessarily take mechanical operation and that may add variability, uncertainty or take extra production steps. The linearity of the dot laser beam can turn a minute into a micro-second. When used with a low-cost photodiode as an on/off detector, the dot or line laser can instantly red flag or even quantify vibration, wobble or mechanical tolerancing of tooling and parts. Alignment feedback loops can automate alignment adjustments or let you know when your tooling is correctly set up and ready to go! This can change your process from money spent into money saved.
Gap Measurement Using Line Lasers
Beyond Borders
Now let’s take a closer look at using a line laser for gap measurement. Gap measurement is an important part of manufacturing control. The presence and size of gaps can have a big impact on the performance of products, especially in the automotive and aircraft industry. Out of control gap tolerances can cause safety risks or engine efficiency loss that rank your automobile too far down the list. Cosmetic problems on the outside tell the customer what’s probably happening on the inside. There isn’t a big market for luxury cars which have lots of wind or vibrational noise along with leaky door seals.
Traditional methods of gap measurement involve mechanical tools such as taper gages, slip gauges and Vernier calipers. These have numerous shortcomings such as low repeatability, a requirement for skilled labor, the need to record measurements and the risk of damage to the measured parts. Using a line laser module as a non-contact measurement solution eliminates these troubles. When used with a camera, this tool measures a gap quickly, providing instant feedback and data that can be logged immediately into process run and control charts.
Line laser technology for gap measurement has been used by manufacturers of aero engines to measure and record the gap between the end of the turbine blades and the casing. This parameter was identified as the leading cause of inefficiency, unreliability and noise production. Monitoring this gap with laser precision enabled an otherwise complex measurement to be made simply so that design improvements could be controlled and quantified.
Automotive manufacturers have also utilized line lasers to improve their output by taking multiple gap measurements of panel fit while vehicles are moving through the production line. This has allowed significantly more measurements to be made without the need to slow down the manufacturing process. Customers experience less vibration and wind noise in a vehicle that looks as good as it performs.
Pattern Generators
Beyond Borders

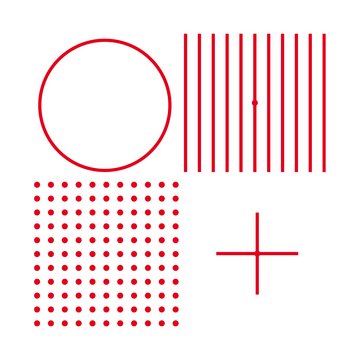
Let’s finally take a look at the use of a diffractive optical element with a laser module. Body shapes on cars, aircrafts and their components have become more advanced than ever with appealing contours and mathematically complex forms. The ability to computer model and design shapes that cut wind resistance and look fantastic mark a new era in intelligent design and manufacturing. It would make sense to use a metrology technique that ensures that a design is brought to its fullest realization. Diffractive optical elements are designed to generate a unique pattern that can help you measure the geometry of your art.
Sometimes a grid of dense lines, a circle, parallel lines or a simple dot matrix will give you the best spatial measurement gage to inspect the form of your manufactured vehicle or aircraft against your computer model. The measured results can put your customer in an automobile or aircraft that looks great and has known superior structural integrity and safety.
FLEXPOINT® MVnano
COMPACT AND FLEXIBLE
The future of mechanical design is at hand and laser modules are the measurement tools that provide the linearity, spatial dimensions and metrological surety that will establish your design as the standard of excellence and the customer’s choice.
The FLEXPOINT MVnano range of line laser modules is an ideal component when designing a non-contact, quick acquisition and data logging sensing instrument. When viewed by a linear detector array or camera the projected laser line is absent across the gap. Once calibrated the absent image can be assigned to the physical width of the gap.
Monitoring such gaps utilizing the FLEXPOINT MVnano aids for such improvements in a much quicker and less skill intensive way than would have been possible using other means.
With three different product variations and numerous options, the FLEXPOINT MVnano module is particularly versatile.
Downloads
Beyond Borders
LASER COMPONENTS Germany - Your competent partner for optical and optoelectronic components in Germany.
Welcome to LASER COMPONENTS Germany GmbH, your expert for photonics components. Each product in our wide range of detectors, laser diodes, laser modules, optics, fiber optics, and more is worth every Euro (€/EUR). Our customized solutions cover all conceivable areas of application: from sensor technology to medical technology. You can reach us here:
Werner-von-Siemens-Str. 15
82140 Olching
Deutschland
Phone: +49 8142 2864-0
Email: info(at)