Laser rangefinder build with APDs and PLDs
THE TARGET IN SIGHT -
LASER RANGEFINDER
The market for laser rangefinders is growing continuously. Developed for high-end applications in the military and industry, laser sensors are more affordable than ever before thanks to their entry into consumer products. At the heart of optical distance measurement are high-quality yet cost-effective laser diodes and photodiodes.
Laser Sensors as a Mass Product
Beyond Borders
Non-contact distance measurement and orientation can already be observed in nature. A well-known example is the bat, which is able to orientate itself in absolute darkness. It uses echolocation to do this; the mammal determines the distance and direction of obstacles from the reflected signals.
Inspired by nature, the search was on for methods that would make such localisation usable for humans as well. These localisation systems can also be used by machines and blind people for orientation. One innovative development from VISTAC, for example, is a so-called laser long cane (Figure 1), which serves as a mobility aid for people with severe visual impairments and the blind. A laser sensor, consisting of a laser diode and detector, is integrated into the cane.
The laser beam is widened in such a way that obstacles are identified that are located exactly above the cane in the head and chest area of the visually impaired person and would not be identified simply by touching them with the cane. If the light reflected by an obstacle is measured, the signalling device begins to vibrate. In this way, similar to our example from nature above, yes/no information is transmitted for spatial orientation.
The automotive industry is also capitalising on this technology and offering more comfort and safety through driver assistance systems. In 2005, more than 40,000 people died on Europe's roads. An e-safety programme launched by the European Commission aims to halve the number of accidents by 2010. Examples of driving safety applications include distance warning systems (see Figure 2), lane guidance assistants and emergency braking systems for vehicles travelling too close.
All information about the driving environment, early warning systems or parking assistants increase road safety. From a legal perspective, the introduction of additional driver assistance systems still requires very careful scrutiny. For example, who will be held liable if a system malfunctions and causes an accident?
This problem does not arise for users who want to measure distances of up to several kilometres quickly and without contact using a modern laser rangefinder. This can be a small, portable laser rangefinder or a rangefinder integrated into a riflescope or binoculars. These systems are used, for example, by golfers who want to improve their handicap or by hunters who want to accurately aim at their target. You don't have to worry about your eyesight either, as the semiconductor laser in the aiming optics fulfils the requirements of laser safety class 1.
The basic element of the laser rangefinder is optical distance measurement based on the principle of pulse time-of-flight ("TOF"). This non-contact tool can be used to measure distances and speeds from a few centimetres to kilometres.
Pulse Transit Time - Functional Principle
Beyond Borders
In time-of-flight measurement, a time-modulated light pulse is emitted in a sharply focussed manner through an optical transmitter. The time of arrival of the reflected light is used to determine the time of flight Δt of the light.
From this, the distance l is determined using the speed of light c. As the light travels the path twice, the distance must be divided by two. The refractive power n of the surrounding medium reduces the speed of light.
The advantage of this method is the short response time. The measuring range for TOF is between 1 metre and several tens of kilometres. The disadvantage is the need to measure at very short intervals (nanoseconds to picoseconds). It is therefore difficult to achieve a resolution higher than a few centimetres. To reduce the time measurement requirements, methods are used in which the laser beam itself is frequency modulated or modulated with a high-frequency signal.
The Laser as a Transmitter
Beyond Borders
Most laser diodes are designed to emit an optical continuous wave power (CW) of a few mW up to several watts. These laser diodes can only be overdriven to a limited extent. If the optical power exceeds the specified maximum value for even a short time, the strong light destroys the internal resonator of the diode.
In contrast, pulsed laser diodes (PLDs) are designed for short, strong overloads and are therefore ideal for time-of-flight measurements. In order to achieve peak performance, the diodes must be driven with a very low duty cycle of typically 0.1 %. This means that a pulse of e.g. 100 ns is followed by a "pause" of 100 µs. To obtain pulse sequences in the kHz range, the optical pulse must therefore be very short. As a rule, pulses of a few 10 ns with very short rise times are generated. To do this, the diode must be operated with a strong current pulse (in the one to two-digit ampere range). Generating such pulses is no easy task. Among other things, it requires special switching transistors and short wiring.
The emitting wavelength is an important criterion when selecting a pulsed laser diode. Depending on the base material used for the active layers, different emission wavelengths can be generated. The 905 nm wavelength, which is invisible to the human eye, has become established for laser rangefinders in the consumer, industrial and automotive sectors. A silicon detector, which has its maximum sensitivity at this wavelength (see below), is suitable as a receiver.
"Multi-Junction" Technology for Maximum Performance
Beyond Borders
AlGaAs is used as the material. The AlGaAs structure of the 905 nm laser diodes has been known for many years for its reliability, beam properties and temperature stability. With an efficiency of 1 W/A, the individual emitters achieve up to 40 W.
Higher outputs can be achieved with the "multi-junction" technology developed by LASER COMPONENTS. Here, several laser diodes are epitaxially stacked in a chip so that the distance between two emitters is only approx. 4 µm. As a result, up to 75 W can be obtained from one diode, depending on the size of the strip. Higher peak powers can only be achieved with stacked structures: Peak powers of 220 W with a pulse length of 100 ns; with shorter pulses, "light flashes" of over 400 W are also possible.
In addition to the wavelength and the electro-optical specifications, reliability is an important criterion for selecting the right PLD. As with other light sources, and semiconductor lasers in particular, the service life of PLDs also depends on the operating conditions. The PLDs can be significantly overdriven with short pulses of a few ns or at low repetition frequencies without being damaged. While a single laser pulse is sufficient for military applications such as the optical detonation of ammunition, security scanners in industry require guaranteed use 24 hours a day for years on end.
The following empirical formula, based on years of experience and measurements, is used to calculate the average failure rate of 905 nm PLDs:
MTTF= k x {P/L}-6x tw-2 x F-1 x f(T)
The following applies:
- Po/L in mW/µm (optical peak power / length of the emitter)
- tw in ns (Pulse length)
- F in kHz (Repetition frequency)
- f(T) = 1 @ 25 °C (Multiplication factor depending on the housing temperature)
- k = Constant, depending on the laser material (e.g.: 1.7 x 1021 for 905 nm PLDs from Laser Components)
The housing in which the PLD chip is installed also contributes to reliability and performance. Until now, price-sensitive applications have had to rely on pulsed laser diodes in plastic housings.
With the 905DxxUA series, LASER COMPONENTS offers low cost / high end pulsed laser diodes in a metallic, hermetically sealed TO56 housing. Depending on the design and chip structure, the peak power ranges from 5 W to 75 W. The advantages of the metal housing with glass window are obvious:
- Glass window enables clean radiation characteristics
- Very precise chip positioning in the housing
- Good thermal behaviour
- Maximum reliability
- Good overdrive capability
- Small inductances and therefore short rise times
The Receiver
Beyond Borders
Silicon PIN photodiodes or avalanche photodiodes (APDs for short) are usually located on the receiver side in laser distance measurement systems in order to detect the short light pulses of the PLDs. These are sensitive in the spectral range from 400 nm to 1100 nm and have their maximum sensitivity at approx. 900 nm. The service life of these components is virtually uncritical. If handled correctly, avalanche photodiodes show almost no signs of ageing.
In conventional PIN photodiodes, incident photons generate electron-hole pairs, also known as charge carriers, which provide a measurable photocurrent. The energy of the incident photons has therefore been converted into electrical energy. APDs go a big step further here. In contrast to ‘normal’ PIN photodiodes, a charge avalanche is triggered when photons are incident on an APD.
Avalanche diodes are therefore particularly suitable for improving sensitivity. The prerequisite is that a reverse voltage is applied to the APD in order to widen the depletion zone. In this zone, the charge carriers released by the light are accelerated in the electric field in such a way that they generate further electron-hole pairs through impact ionisation. The current generated is calculated as follows:
(a) I = Ro x M x Ps
where Ro (A/W) is the spectral sensitivity of the APD, M is the internal gain and Ps (Watt) is the incident light power. The amplification of the APD depends on the applied reverse voltage.
APD or PIN-Diode
Beyond Borders

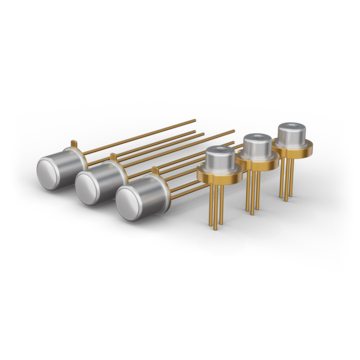
To compare the performance of an APD with a PIN diode, it is not sufficient to compare the noise of the detectors alone. The decisive factor is the signal-to-noise ratio of the entire system. In the case of PIN diodes, the associated preamplifier, whose noise characteristics are frequency-dependent among other things, must always be taken into account in the assessment. An APD is always superior to a PIN diode if the APD can significantly amplify the signal level without significantly increasing the overall noise of the system. APDs are favoured where low light intensities are detected at medium or high frequencies.
To ensure that the APD does not affect the system noise, the internal gain must be controlled so that the detector noise is approximately equal to the input noise of the downstream amplifier or load resistor.
The internal gain is optimised when the detector noise is approximately equal to the input noise of the downstream amplifier (or load resistor) so that the APD does not affect the system noise.
In terms of the application, an APD achieves an improvement in the signal-to-noise ratio by a factor of 2 to 5 compared to PIN diodes with preamplifiers due to the internal amplification of approx. 10 to 1000. With both PIN diodes and APDs, the noise increases with the bandwidth of the system. It should therefore be carefully checked what options are available to reduce the bandwidth.
To avoid noise caused by ambient or stray light, a suitable optical bandpass filter is placed in front of the receiver. With the SARF500F2, Laser Components also offers a high-end / low cost solution for the combination with 905 nm pulsed laser diodes. In the SARF series (Fig. 6), a 905 nm bandpass filter is already integrated in the small TO housing. The 230 µm or 500 µm APD chip is also optimised for 905 nm, so that optimum performance at 905 nm is guaranteed. The advantages of integrating the filter directly into the housing include Cost savings, as an external filter is no longer required and additional assembly steps are no longer necessary, the smallest design and optimum system properties at the 905 nm measuring wavelength. The APD filter solution is manufactured in a modified TO-46 or as an SMD housing.
Summary
The applications for laser sensors are continuously increasing. Low-cost/high-end components such as pulsed laser diodes in metal housings and avalanche photodiodes with built-in bandpass filters are now used in the manufacture of cost-effective laser rangefinders based on the time-of-flight (TOF) principle.
Literatur
Laser Components: „Silicon Avalanche Photodiodes“
Vistac: “Laser Langstock” www.vistac.de
K. Fürstenberg & R. Schulz: Laserscanner für Fahrerassistenzsysteme, ATZ09/2005 Jahrgang 107
www.wikipedia.de
Product Selection
APDs and PLDs for Laser Rangefinding
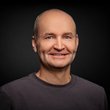
Click here
LASER COMPONENTS Germany - Your competent partner for optical and optoelectronic components in Germany.
Welcome to LASER COMPONENTS Germany GmbH, your expert for photonics components. Each product in our wide range of detectors, laser diodes, laser modules, optics, fiber optics, and more is worth every Euro (€/EUR). Our customized solutions cover all conceivable areas of application: from sensor technology to medical technology. You can reach us here:
Werner-von-Siemens-Str. 15
82140 Olching
Deutschland
Phone: +49 8142 2864-0
Email: info(at)