Sustainable Laser Cleaning without Chemicals
A Clear Beam Profile Ensures the Highest Precision
Many production steps in modern industry require clean, precisely pre-treated materials. For example, the surface condition is important for the embossing structure of printing rollers in the paper industry. One other application is, for example, the degreasing and microstructuring of rotor shafts in electric mobility.
If components are to be bonded to metal surfaces, not only do the oxide layers have to be removed in advance but their surface also has to have exactly the right amount of roughness in order to achieve stable, reproducible, and process-reliable adhesion with the selected adhesive. It is precisely in this area that cleanLASER technology has made “quantum leaps in quality.” The laser can also be used in marking glass and removing coatings, for example to generate transmission points on windshields for GPS transmitters and radio reception.
Lasers Clean “Gently” and Quietly
Beyond Borders

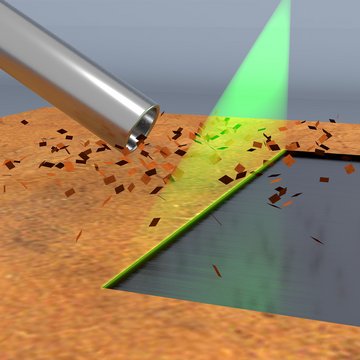
The coating should be completely or partially removed from other parts. In the past, aggressive chemicals such as acids or alkalis were used for this purpose. The handling of these hazardous substances requires elaborate safety precautions, and then there is always the question of disposal. Alternative methods such as particle blasting are associated with noise and dust generation. Furthermore, conventional cleaning methods often attack the base material in addition to the undesirable coating.
For many applications, laser cleaning is therefore an attractive alternative: Precision, automation, and reproducible results guarantee the desired quality. Moreover, there are the environmental aspects to consider: Energy consumption of a few kilowatt hours and the fact that cleaning media are not required make the laser process the most sustainable cleaning technology on the market.
Layers as Thin as Possible
Beyond Borders
Basically, the cleaning process is based on the principle of laser ablation. In this process, material is strongly heated by a short laser pulse. Since heat conduction is a very slow process, the thermal movement of the atoms remains concentrated at the focal point of the laser, which leads to higher temperatures.
As a result, the heated material layer can suddenly be vaporized and extracted. If the laser beam reaches the basic substance – which is usually a metal in industrial cleaning – it is reflected by the surface and remains undamaged. It is crucial that the wavelength, pulse duration, and shape of the laser beam precisely match the base material and the layer to be removed. A “sledgehammer method” that is equally successful in all applications does not exist here.
In automobile production alone, laser cleaning has significant advantages in around 30 areas. These areas include the adhesive pretreatment of engine seals, structural parts, and control units, as well as the welding and soldering pretreatment of gear wheels, aluminum bodies, and airbags. Paint must be removed from stabilizers and contact points for the ground wires on the car body. Electromobility is adding further fields, especially in the manufacture and assembly of batteries.
Uniform Power Distribution
Beyond Borders

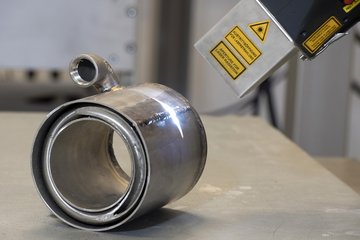
While most laser applications use a laser beam with a Gaussian intensity distribution, laser cleaning requires the homogeneous illumination of a comparatively large area of just under one millimeter. There the laser power should be distributed evenly across the material. A so-called top hat profile, in which the beam comes out of the optics bundled like a top hat and hits the material with a clearly defined edge, is optimal. This shape can be achieved with diffractive optical elements (DOEs): These include glass carriers into which complex microstructures are etched. Targeted phase modulation in these microstructures generates the optimum intensity profile by interference in the working plane of the laser.
Together with our partner Holo/OR we offer you a wide range of diffractive optical elements for lasers of all power classes and wavelengths. The range extends from classic multi-spot beam splitters to complex designs for beam shaping and profile change. Our experts will be happy to work with you to develop the perfect beam profile for your application.
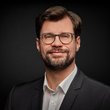
Click here
Product
Beyond Borders
LASER COMPONENTS Germany - Your competent partner for optical and optoelectronic components in Germany.
Welcome to LASER COMPONENTS Germany GmbH, your expert for photonics components. Each product in our wide range of detectors, laser diodes, laser modules, optics, fiber optics, and more is worth every Euro (€/EUR). Our customized solutions cover all conceivable areas of application: from sensor technology to medical technology. You can reach us here:
Werner-von-Siemens-Str. 15
82140 Olching
Deutschland
Phone: +49 8142 2864-0
Email: info(at)