Optoelectronic personal protection
OPEN SESAME
The fact that doors open and close by themselves in the supermarket, in the hotel lobby or on the suburban railway is now so commonplace that hardly anyone thinks about how they actually work. Sophisticated intelligent sensor technology is often behind this, which is not only convenient, but also prevents serious accidents - and LASER COMPONENTS supplies the optoelectronic components to ensure that everything works smoothly.
FROM THE SIMPLE LIGHT BARRIER TO THE LIGHT CURTAIN

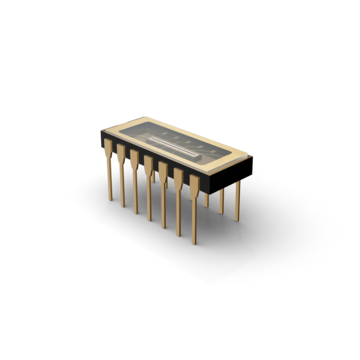
The simplest system is the well-known one-way light barrier, which recognises obstacles at a certain height: controlled by electronics, a light source constantly emits a beam that is received by an opposing detector. In the case of sliding doors, light sources with infrared radiation, which is invisible to the eye, are used for this purpose. The beam is usually located at ankle height. As soon as it is interrupted, the receiver gives the feedback signal "obstacle" and the door opens for a while.
This safety device is usually sufficient for ground-level doors. In other situations, however, the light barriers are often combined with additional safety mechanisms. When boarding many trains, for example, a step has to be negotiated. Older passengers, in particular, hold on to the handrail before stepping onto the first step. If the light barrier is only installed at ankle height, the door may close prematurely and the passenger's arm may become trapped. Additional technologies such as pressure sensors or further light barriers can prevent such situations.
So-called light curtains are also increasingly replacing simple light barriers. Many transmitter and receiver units form a fine line grid so that nothing can get caught in a sliding door. Light curtains are also widely used in industry, where they ensure, for example, that machines are stopped as soon as someone enters the danger zone.
COMPLEX SENSORS FOR REVOLVING DOORS
Beyond Borders

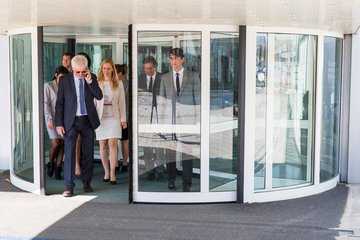
Revolving doors inhibit draughts and thus save energy costs. This is why they are often used in hotels or large office buildings. Here, the safety requirements stipulated in DIN18650 are considerably more complex than for sliding doors. Electronic distance measurement is intended to provide additional safety and prevent people from being trapped or getting stuck in the swing doors. Two optoelectronic methods are the most common: the cost-effective triangulation method and the use of complex laser scanners with time-of-flight measurement.
DISTANCE MEASUREMENT
by means of triangulation methods
The triangulation method is mainly used for automatically rotating revolving doors: If someone stops in a door leaf, the door stops turning.
The principle is similar to that of a light barrier, but sensors are used as receivers that make it possible to determine the position - for example PSDs (Position Sensitive Detectors) or CCD cameras.
In simple terms, the sensor continuously measures the distance to the ground. As soon as the measured distance decreases, an obstacle is recognised and the door system is stopped.
OBJECT RECOGNITION
WITH LASER SCANNERS
When maximum precision and speed are required, laser scanners come into play. They are used as anti-trap protection on revolving doors and in industrial applications to protect against machinery: the sensors detect intrusion into a dangerous area and trigger a (machine) stop.
Laser scanners work according to the principle of optical time-of-flight measurement. In the typical setup of industrial laser scanners, a rotating mirror is used to scan a two-dimensional surface in order to capture the surroundings (see illustration). The systems achieve a high angular resolution, which enables precise and detailed distance measurement.
Industrial laser scanners typically cover an angular range of up to 270°. The automotive industry even uses systems that cover 360° for autonomous vehicles. With a three-sided mirror, the scanning surface is scanned three times per rotation. If the mirror surfaces were tilted, it would even be possible to scan inclined planes instead of a purely two-dimensional surface.
SUITABLE TRANSMITTERS AND RECEIVERS
FROM A SINGLE SOURCE
Laser scanners are used to monitor very different distance ranges. Pulsed laser diodes (PLDs) are used as the light source. The shorter the distance to be measured, the smaller the pulse width. Typical versions are << 10 ns. At long distances, however, the pulse power must be high enough to be able to detect the returning signal.
LASER COMPONENTS manufactures customised pulsed laser diodes in Canada. For distance measurement, 905 nm PLDs are usually requested. Various detectors are used as receivers, including avalanche photodiodes (APDs). APDs also receive weak light signals and are therefore the preferred choice. The production facility for the photodiodes in Arizona is also strong in the development of customised detectors and the APD arrays, which are ideal for laser scanners, are outstanding.
Selecting the right components is a basic prerequisite for accurate and reliable distance measurement. What sounds simple can often become a pitfall: You can therefore rely on the specialists at LASER COMPONENTS - in addition to developing and manufacturing the components, our experts provide comprehensive advice and are also aware of the importance of the source and receiver circuitry.

Click here
Download
Beyond Borders