High Quality Standards in Laser Module Production
Mechanical engineering is one of the industries in which automation and digital transformation are having a particularly strong impact. Mechanical precision has long been combined with sophisticated data technology. In many applications, today’s machines can be classified in the category of human-machine interaction. Some see them more as mechatronic hybrid beings with their own senses and their own goal-oriented intelligence. The role of the eyes is played by digital image processing (machine vision): structured laser beams scan surfaces and objects, a camera records the reflected light, and software uses the results to calculate how the machine should proceed. As application requirements become more complex, production becomes more demanding, especially regarding laser modules for machine vision. Miniaturization has long since taken hold in this area as well. Of course, the small components should deliver at least the same performance as their larger predecessors. As in all production areas at LASER COMPONENTS, the same applies here: The application determines the product specifications. LASER COMPONENTS and its subsidiary Blau Optoelektronik GmbH supply such custom MV solutions, as well as standardized laser modules (e.g., as positioning lasers).
No Two Modules Are Alike
Beyond Borders

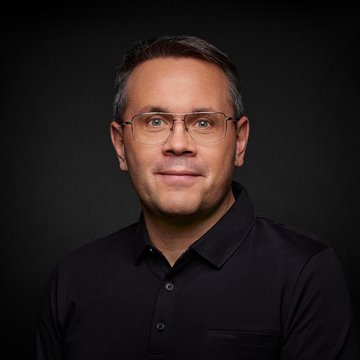
Regardless of the industry, we consider each laser module individually based on the practical benefits to be achieved by the application. Our product engineers know which specifications will enable the customer to implement his ideas in the best possible way. Wavelength, beam profile, power, housing, connection, and power distribution are individually adapted to these requirements.
We also develop customized solutions “from scratch” upon request. Our in-house development team brings together physicists and engineers from different disciplines who work closely together combining products and processes. Their various specializations enable them to pursue even unusual approaches and develop application-specific solutions.
Picture: Jochen Maier, head of the optosystems business unit, gives us an overview of the different application areas and their requirements.
Eye Safety for Medical Applications
Beyond Borders
In addition to industrial image processing, our FLEXPOINT® modules are also used in many medical systems (e.g., as positioning lasers in magnetic resonance tomographs and other diagnostic procedures). To obtain the sharpest possible images, examinations are usually performed under a low level of anesthesia.
This slows down the blink reflex, which the body uses to protect the eye from strong light. Therefore, all modules must ensure laser class 1 eye safety. To guarantee reliable laser class categorization, each FLEXPOINT® model is measured by us according to DIN EN 60825-1 and assigned the appropriate laser class. The measuring stations are certified at regular intervals by external experts. We gladly go the extra mile to ensure patient health and safety.
Successful with Practice-oriented Models
Beyond Borders

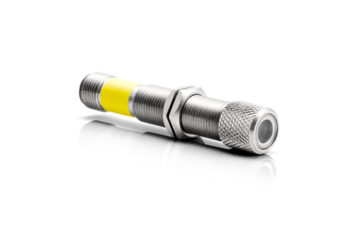
Sometimes success is simply a matter of intelligent, practice-oriented product development. This can be seen in the example of the ILM12F series, in which the housing is made of stainless steel and has an M12 thread.
This allows the modules to be integrated quickly and easily into a wide variety of industrial positioning and alignment systems. This product series, which was expanded a few years ago to include the dustproof and waterproof ILM12IP model, has become an absolute mainstay.
In view of the global pressure to innovate in the industry, these modules are becoming increasingly popular, especially in international business.
High Quality Standards
Beyond Borders

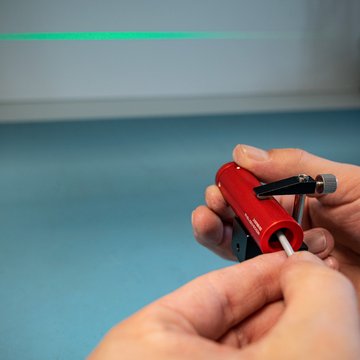
The highest quality standards do not just apply to eye safety. During production, beam quality, focus, and alignment are checked in each individual module. After all, the product is expected to meet the given specifications over a long period of time. This also means that the overall system, which consists of a diode, electronics, and a housing, must have a correspondingly long service life. To this end, selected FLEXPOINT® models undergo an accelerated service life test during the development phase: In a climatic chamber, the aging process is simulated under various thermal conditions.
Launching an Offensive for Consistently High Quality
Beyond Borders
With such a diverse range of products that must meet the requirements of very different industries, uniform, cross-location quality assurance is especially important. LASER COMPONENTS and Blau Optoelektronik are pursuing this goal with a joint failure mode and effects analysis (FMEA) project. The system analysis is the basis of such considerations. For this purpose, the manufacturing process was put under the microscope.
The assignment of process parameters and potential sources of error initially makes it possible to evaluate the process steps in terms of their weak points. Appropriate measures can then be taken to eliminate these weak points. In this way, we can ensure that every customer order is processed as quickly as possible and that FLEXPOINT® modules from both production sites always meet the highest quality standards.
Our Partner for High-quality Laser Modules
Beyond Borders

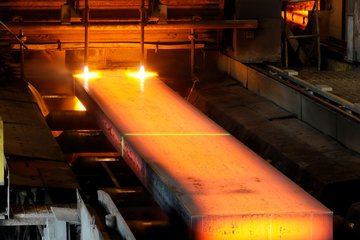
Blau Optoelektronik GmbH was founded in 1987 by Frank Blau. The company is located in Überlingen on Lake Constance and benefits from Blau’s many years of experience as a developmental engineer for laser technology in the aerospace industry. Pioneering achievements in the development and manufacture of laser pointers laid the foundations at that time for today’s dot, cross-hair, and line laser modules.
Since then, the product range has been continuously expanded, initially to include triangulation-based laser distance meters and laser transmitting and receiving systems. Later, microcontroller systems were also added. Since 2012, Dr. Ingmar Blau and Eugen Romasew have been at the helm of the company as managing directors.
Downloads
Beyond Borders